在金属加工领域,对于管线钢材的性能提升需求日益增长。高频调质淬火生产线应用于管线材在线淬火热处理,凭借其高效、节能的显著优势,成为优化管线钢等材料强度与韧性的关键工艺,为现代工业输送优质管线钢材。
高频调质淬火生产线基于电磁感应原理运作。当高频电流通过环绕管线材的感应线圈时,瞬间产生高频交变磁场。处于该磁场中的管线材,因其良好的导电性,内部迅速产生感应电流(涡流)。由于管线材自身电阻的作用,电能快速转化为热能,使管线材表面及一定深度范围内迅速升温。在达到合适的淬火温度后,通过特定的冷却系统,如喷淋装置,对管线材进行快速冷却,实现淬火过程。而调质处理则是在淬火后,通过适当的回火工艺,进一步调整管线材的组织结构,以获得理想的综合力学性能。
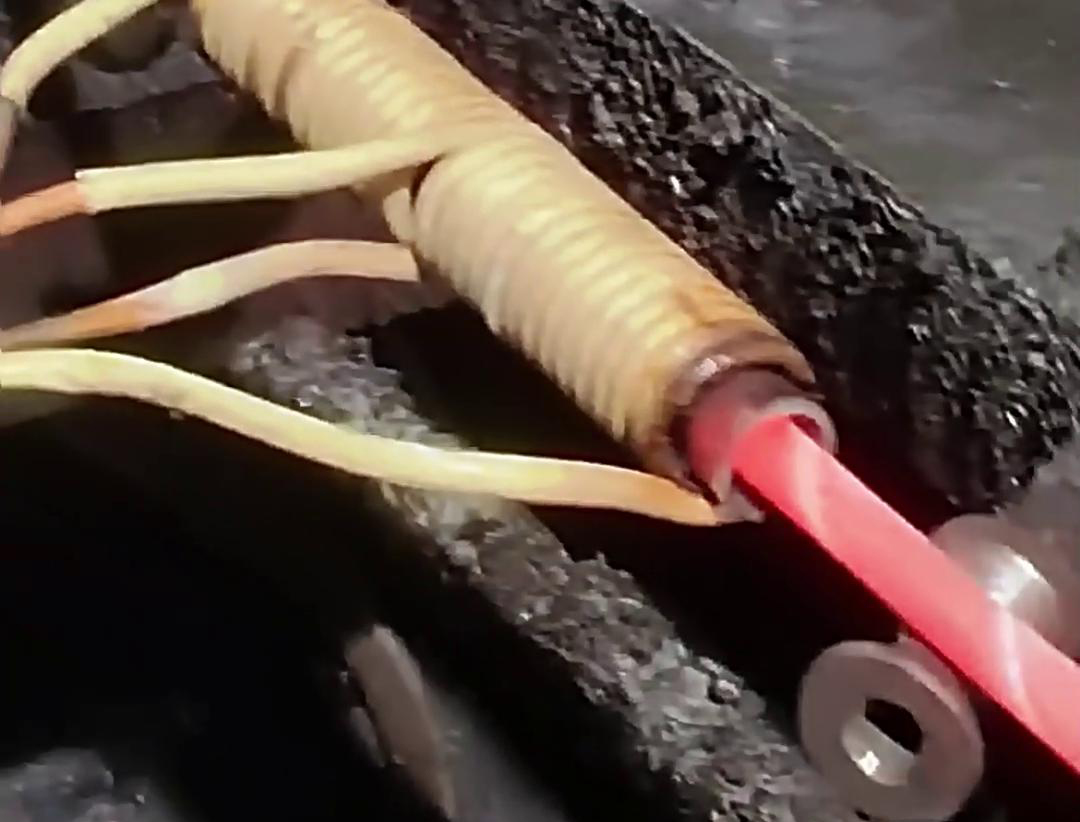
高频调质淬火生产线的加热速度极快。相较于传统的加热方式,如燃气加热或电阻炉加热,它能在极短时间内将管线材加热到淬火所需温度。例如,对于常见规格的管线钢,使用高频加热可在短短数秒内使表面温度达到 800 - 900℃,满足淬火工艺要求。这种快速加热特性大幅缩短了生产周期,使管线材能够在连续生产线上快速通过热处理环节,实现高效的在线生产。在大规模管线材生产中,可显著提高单位时间内的产量,满足市场对管线钢材的大量需求。
该生产线能够实现管线材的连续在线热处理。管线材在生产线上持续移动,依次经过加热、淬火、回火等工序,无需停顿或进行复杂的转移操作。这种连续作业模式避免了传统间歇式热处理方式中频繁的装炉、出炉过程,减少了生产过程中的时间浪费和能源损耗。同时,保证了产品质量的稳定性,因为连续的热处理过程可使每一段管线材都经历相同的工艺条件,减少了批次间的质量差异。
高频加热是基于电磁感应在管线材内部直接产生热量,热量散失少,能量利用率高。与传统加热方式相比,传统加热方式在加热过程中,大量的热量会通过炉体、空气等途径散失,造成能源的浪费。而高频调质淬火生产线的能量利用率可达到 70% - 80%,相比传统加热方式可节能 30% - 50%。这不仅降低了企业的生产成本,还符合国家节能减排的政策要求,为企业的可持续发展提供有力支持。
高频调质淬火生产线配备先进的温度控制系统和自动化监测设备,能够精准控制加热温度、时间和冷却速度等参数。通过精确的参数设定,可确保管线材在达到理想的热处理效果的同时,避免过度加热。例如,在淬火过程中,当管线材达到预设的淬火温度时,系统自动调整加热功率,防止温度过高导致的能源浪费和材料性能下降。这种精准控制能力在保证产品质量的同时,进一步提高了能源利用效率。
经过高频调质淬火处理后,管线钢材的组织结构得到优化,形成了细密均匀的马氏体组织,同时在回火过程中,马氏体组织进一步分解和沉淀强化,使管线钢材的强度显著提高。例如,对于 X70 级别的管线钢,经过高频调质淬火处理后,其屈服强度可提高 10% - 20%,能够更好地承受输送介质的压力,满足高压、大口径管线的使用要求。
在调质过程中,通过合理控制回火温度和时间,能够有效调整马氏体的形态和分布,减少内应力,提高管线钢材的韧性。高频调质淬火处理后的管线钢,在保持高强度的同时,其冲击韧性也能得到明显提升,如夏比冲击功可提高 20% - 30%。这使得管线钢材在面对复杂的地质条件和环境载荷时,具有更好的抗断裂能力,提高了管线的安全性和可靠性。
高频调质淬火生产线在管线材在线淬火热处理中展现出卓越的高效性和节能性,为提高管线钢材的强度和韧性提供了可靠的技术手段。随着工业对管线钢材性能要求的不断提高,该生产线有望在更多领域得到广泛应用和进一步发展,推动管线钢材生产技术的持续进步。